What does it require to perform key maintenance on the unique fjord cooling solution at DC1-Stavanger? Five professional divers? A vacuum truck? 20 professionals from Green Mountain and suppliers? And a week’s downtime? The answer is: All of the above except the downtime, of course. Let us explain the process…
Cooling form the deep fjord
First, let us just clarify what a fjord cooling solution is. At Green Mountain’s DC1 data center we truly make use of the natural conditions to cool our client’s data servers. Adjacent to our mountain hall facility is a deep-water fjord. Here the water temperature at 100 meters depth is constantly 8˚C. (48F) We can use this cold water to cool down our entire facility. Here is how it works: The water enters our cold-water basin through use of gravity only. From pipes reaching 100-meter depth. Further, this chilled 8˚C water circulates through a titanium heat exchanger. Finally, the water is discharged back into the fjord. In this closed loop system, the chilled fresh water circulates around the facility via redundant/compartmentalized paths. This means that there is no extra water usage. Furthermore, the heated sea water discharged back into the fjord has no negative environmental impact either.
Meticulously planned maintenance process
Although humans and sensors supervise the cooling solution on a daily basis, once in a while it needs a more thorough inspection. Being a data center, we are dependent on reliable cooling 24/7 all year round. That is also why our cooling solution is fully duplicated, providing a N+N solution. Normally, both systems are active in operation. However, in order to perform concurrent maintenance we had to plan to take one of the systems out of operation.
Planning a key maintenance operation like this actually starts 6 months in advance. It is the operations department who is responsible for the task. A detailed plan is produced and all the relevant personnel, both internally and from equipment vendors, must be convened. Above all, the maintenance must be carried out in a safely manner, both for the personnel and for operation.
For example, before we could send a diver down in the water basin to close the fjord water entrance, a careful plan was created. There was a thorough briefing before the operation could start and testing of both equipment and communications. The diving supervisor always had audio- and visual contact with the diver through radio and video. “Personnel safety is always our number one priority. Clear and concise communication is important, especially when staff from different organizations cooperate. This way we minimize the risk of potentially unsafe situations. You should be as healthy when you go home from work as when you came to work.”, says Bjarne Sørbø, DC Design & Operation Specialist at Green Mountain.
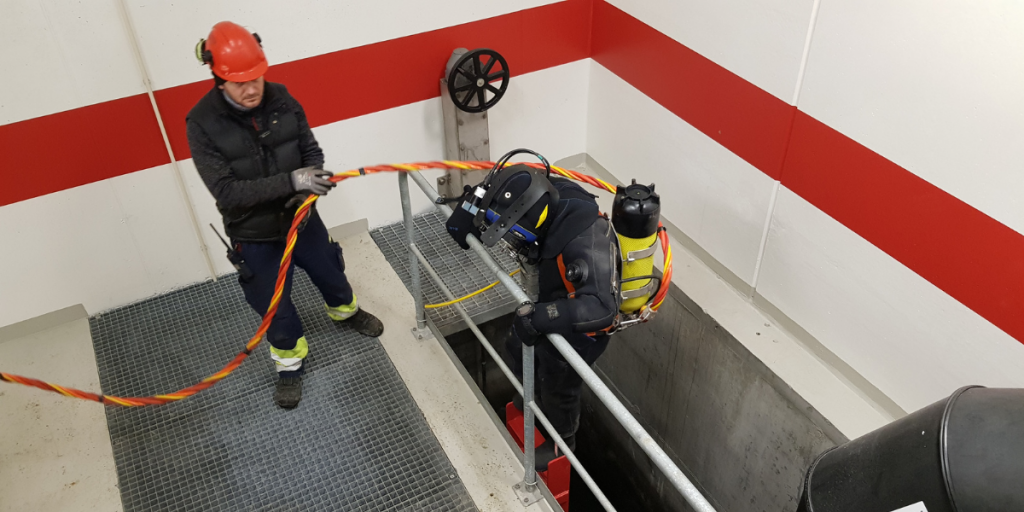
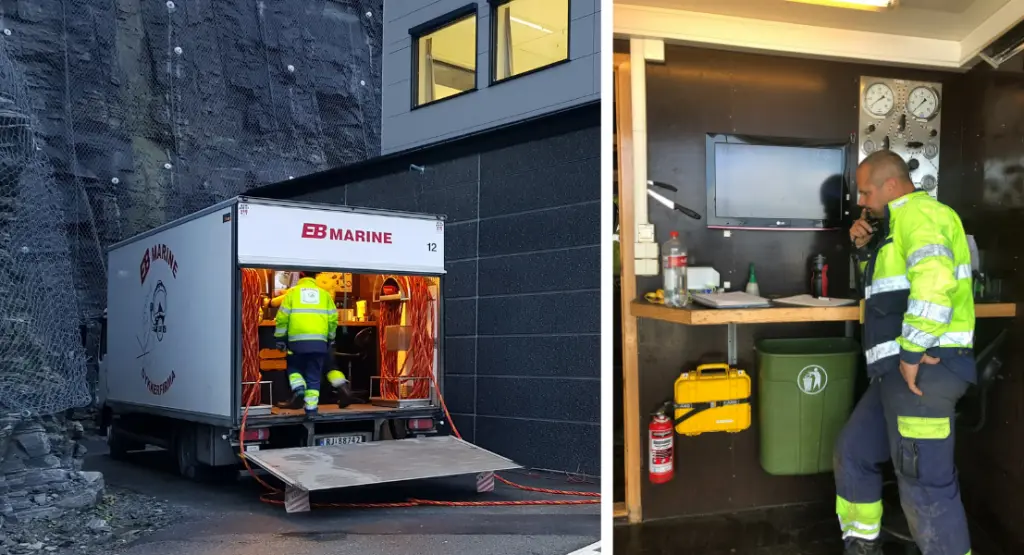
Maintenance operation – step by step
So, what did we actually do? These were the main steps of the maintenance process of the cooling solution:
- Transfer production from a duplicated cooling systems to a single system
- Use divers to reach the bottom of the water basin to mount a lid to prevent seawater from accessing
- Drain the water basin
- Clean the water basin of sediments and sludge with a vacuum truck
- Inspect all components in the seawater circuit
- Replace all valves
- Overhaul the pumps
- Test and restart the system
It took 4 days to complete all the tasks. Testing and documentation of every step of the process was a vital part. In short, we discovered no major faults, leaks, or deficiencies, but it is still important to go through this process at regular intervals. A well-maintained system avoids errors and makes operations easier.
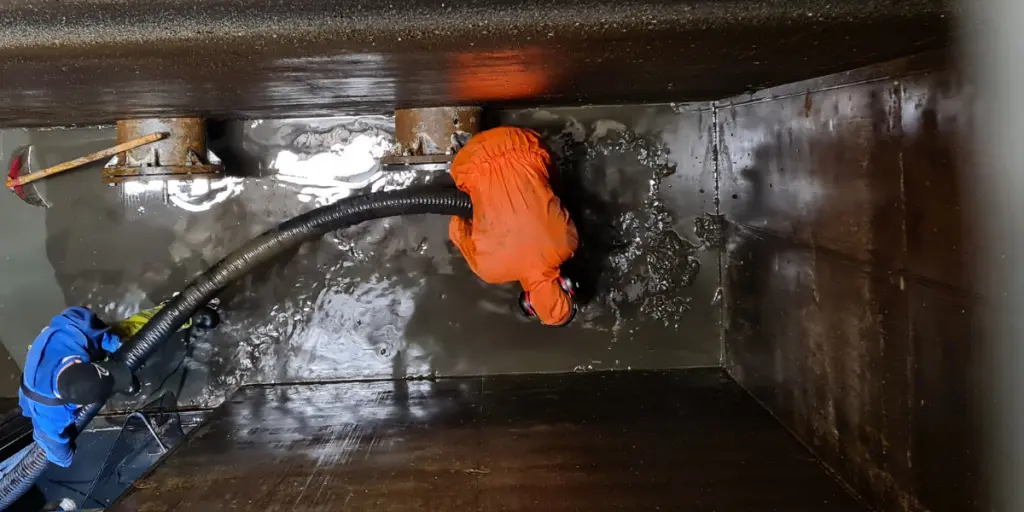
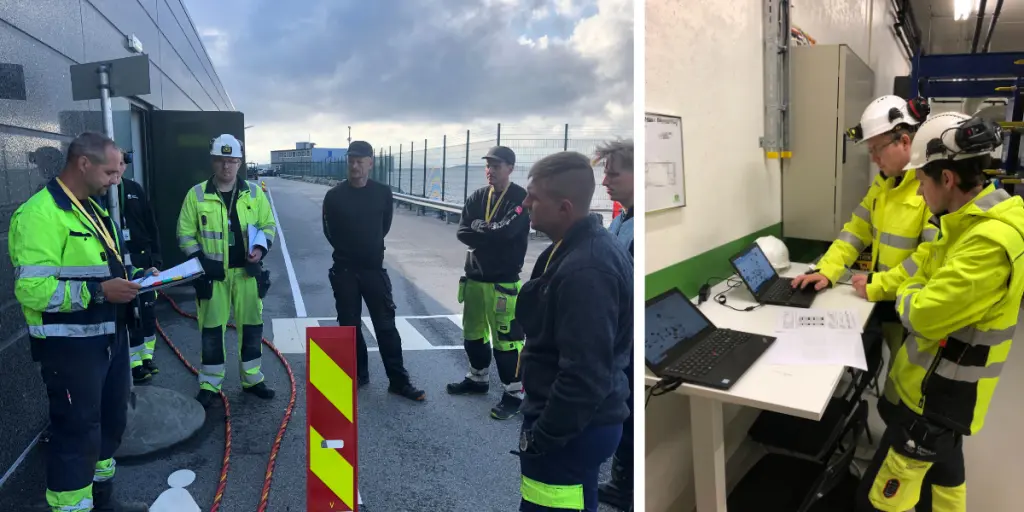
Excellent teamwork
Jim-Aage Johansen, Operation Manager DC1, has been responsible for the technicians at Green Mountain and the execution of the plan. He is very proud of the team effort. “In a procedure like this there are a lot of people involved. Apart from the Green Mountain employees, workers form four external companies had specific roles in the process. I am very pleased with the level of professionality from all parties involved. The operation went smoothly. Most importantly, there were no HSEQ incidents. We can now rest assured that the cooling solution still operates flawlessly.” he says.
Fjord cooling solution – the heart of the facility
The next step for the team is of course to repeat the whole process on the duplicated cooling system. In other words, as a Tier-III certified data center there is no room for downtime. Both systems must be in tip-top shape. “The cooling solution is in a way the “heart” of the data center facility. We are particularly proud of our unique system. Normally, cooling a data center accounts for an additional 40-80% of the electricity required to power the servers. Here at Green Mountain, we can use the natural conditions of the cold fjord to our benefit. This solution reduces the power consumption substantially.” says Sørbø.
Working in a data center involves a range of varied tasks. But, for the operation technicians at Green Mountain, maintenance projects like these are some of the highlights.